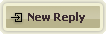 |
|
05-17-2010, 05:30 PM
|
#201
|
Senior Member
Join Date: Apr 2009
Posts: 212
|
Bob, I think you must be right. During the normal tape and mud process for sheet rock the gaps between the boxes and the sheet rock get filled with mud (spackle). In my case, with the plywood I didn't do taping, though I did use caulk and non-shrink spackle in a somewhat similar process. I didn't realize that I needed to fill the gaps around the boxes until I started to put the covers on and noticed the gaps. I had caulked around the bozes, but didn't fill them to flush with the spackle. At any rate, I have done so now, so all visible gaps are gone.
I think you are also right about the outlet ears, but in my case they never reached the plywood. Had I pulled the wires and then done the spackle, they would have reached the spackle, but I put the outlets in before I did the caulk and spackle process. As usual, I cost myself time and effort, but I got it done.
As for the outlet spacers, I have seen them as well. I couldn't find them when I was looking this last time, so I just made my own out of wood. In most cases I didn't need them anyway, except for a couple of boxes where I screwed up and mounted the box way too deep.
As of yesterday, all outlet and box covers are installed, even the ones in the ceiling that enclose the antenna amplifiers. I also installed the crank and pointing handles for the two antennas.
I also did some finish painting around the doors and finally installed the peep hole. I set it as low in the door as felt comfortable, but I probably should have set it even lower. Even with the wide angle of view I will only just be able to see the head of someone standing a reasonable distance outside the door. The inside of the truck is just so much higher than ground level, it makes for quite a compromise on the placement of the peep hole and the door handle.
__________________
|
|
|
05-24-2010, 08:53 PM
|
#202
|
Senior Member
Join Date: Apr 2009
Posts: 212
|
Milestone Managed
I finally have a clean empty room. It doesn’t sound like much, but the inside of every outer surface, walls, ceiling, floor, doors, are all done.
After laying the plywood floor I caulked the gaps and edges just like the walls. At first I tried to use standard floor leveling compound, to fill the screw holes, but that stuff has heavy grit sand in it. I really didn’t like the way it was working, so I ended up using standard wallboard joint compound. It took two coats to fill the screw holes due to shrinkage, and a little light sanding, but the floor was perfect.
This weekend I put down the vinyl flooring, nothing fancy, just a simple wooden floor board pattern. I was looking at vinyl at up to $4.00 per square foot, but in the end I decided to go with the $1.00 per square foot stuff. I brought a sample home and stomped on it, threw dirt on it, ground my heel into it, threw more dirt on it. I even tried sanding it with my silicon carbide sanding block. All I managed to do was dull it a bit. I put a coat of that floor sealer on it that I mentioned earlier and it was good as new, so I figured, why spend more?
The process of laying the vinyl was made simple by the fact that I was installing it in an empty room. It was almost a simple rectangle. I made a paper template, but it was almost unnecessary. I laid out the flooring in my current living room. It’s a sobering fact to note that my entire future living space fits in my current living room without removing much more than the coffee table. That’s 13’11” by 7’4” to be exact.
Gluing it down was more exciting than it should have been. I calculated that I needed 3 quarts of glue, so I bought a gallon. About 3/4 of the way through the job, you guessed it, I ran out. That was followed by a mad dash to the hardware store for more glue and rushing back to try and finish the job before the first of the glue had a chance to set. I got it done but it was a little silly. I suggest you buy twice what you need and then keep the receipt. You can always give it back if it is unopened.
Putting the glue down with a notched trowel, I wanted to get it all the way to the edges by the walls. Naturally the trowel would rub up against the walls and leave sticky glue all over them. In most installations this would be covered by the base board so it wouldn’t mater, but in my case there is no base board, just a bead of caulk at the bottom corner.
My plan was to scrape it off, or possibly take it off with lacquer thinner the next day, after the floor had a chance to set up a bit. Either one would have damaged the paint and forced some touch up, but I found a better way. It turns out the dried glue sticks to itself just slightly better than it sticks to the wall, your fingers, etc. I just started grabbing the glue and pulling it off the walls. At first it would not come loose, and would stretch out like incredibly sticky taffy, but gradually I had a wad of it well and truly stuck to my fingers. I could then “dab” or “poke and pull” that wad into the glue on the wall. Every time I would pull back a bit more of the glue was in the wad, and in the process ever more firmly stuck to my hand.
After about 5 minutes I would have to transfer the glue from one hand to the other, and then use the poke and pull technique to clean the glue off my first hand. That would allow me to clean another few feet of wall until I had to swap hands again. The perimeter of my small room probably took an hour and a half to clean, but it left the walls spotless with no damage to the paint. By that time I felt like Brer Rabbit with a Tar-Baby the size of a large egg.
The next day I opened up all the holes in the floor with an X-acto knife. It wasn’t hard to feel the soft spots in the flooring and make the first cut inside of the opening by about 1/4”. Once I could see the holes better it was easy to use the knife to follow the opening walls and finish the cut.
The lid over the floor safe was a bit more challenging. It’s a plywood rectangle with rounded corners, about 2 1/2” in diameter. I cut it at an angle, like the top of a jack-o-lantern and it just sits in place, flush with the floor. I glued the flooring right over it for a perfect match. There is just one little hole, about 1/4” where I started the jig saw cut and that was a little hard to find by feel. Once I got the knife blade in the slot a single pass around the lid freed it. Now the lid drops back in and the cut almost disappears. The only thing you can really see is that little 1/4” hole, which is also a place to get a finger tip in to lift the lid. The whole thing will be under the bed so you will have to lift the mattress and the mattress base to get at it. It’s not meant to be convenient so much as well hidden.
Some 1” aluminum L channel by 1/16” thick finished off the threshold at the rear door. A little caulk around the edges and it’s done. I even put down a layer of that floor sealer I mentioned earlier to help protect it from the abuse I will no doubt give it while finishing out the build.
The next step is to mount all the gas appliances, meaning the toilet, range, and heater. I will put them in, fully test everything, and then take them out again before installing the cabinet walls. I figure it will be a lot easier to finish out the plumbing now that everything is wide open. I can also hard mount everything to the walls or floor. Mostly that is just a matter of lag bolts into the floor for the toilet and smaller screws into the wall for the heater, which is small and light. The range will have to have brackets built into the floor so it can be slid straight back into its pocket between the cabinets and have the feet catch and hold. I have a rough plan, but these things tend to change at the point of implementation.
The one thing that worries me is the toilet flue. I hope to gosh I measured everything correctly because the roof opening, flue cap, and everything is already in place. It will either drop in perfectly, or I will be swearing.
You can find several new pictures under keyword "Stealth".
To be continued…..
__________________
|
|
|
05-25-2010, 12:48 AM
|
#203
|
Senior Member
Join Date: Apr 2006
Posts: 625
|
.....FLOOR FINISH IDEA:....LINEX= EXPENSIVE BUT THERE ARE OTHER BRUSH ON PRODUCTS AS WELL.....AND BEING A SCORPION DEALER MY COST IS ABOUT $2.00 A SQFT.....IT COMES IN COLORS AND HAS VARIOUS ADDITIVES TO CHANGE THE TRACTION ISSUE SHOULD YOU NEED TO HAVE SOME SLIP PROOF AREAS......I SELL THE HELL OUT OF THE FLOORING TO THE DIRT BIKERS THAT WASH OUT THEIR TRAILERS WITH A WATER HOSE AND AIR DRY WITH A LEAF BLOWER....AGAIN TO KEEP FROM MY OLD BONES BREAKING I USE WALK OFF MATS THAT ARE ABOUT $15.00 FOR A 5x3 AT WAL-MART IN DARK GRAY.....NO SLIP NO FALL AND THEY WONT SLIDE AROUND.....EASY TO CLEAN WITH A HOSE AND HANG UP ON A FENCE IN THE SUN.......geofkaye and the Rivercity Group
|
|
|
05-25-2010, 10:14 AM
|
#204
|
Senior Member
Join Date: Mar 2008
Location: West Fargo ND
Posts: 300
|
The project looks like its in the "Home" stretch, man I wish you would have started off with a bigger truck, I see all this well thought out work you have put into this project, the planning, the expense, the labor. I truly hope that you will be happy in such a confided space.
I know from our build, that there are many things I'd change on the next one, but I wonder how I'd get even close to re-couping my cash costs or even a good percentage of them, if I was to sell. I think you may find yourself in the same spot, too much invested to sell and not content to keep it. I hope I'm wrong, you seem to plan things very well. Perhaps this is the exact choice of "home" you had in mind.
I wish you happiness and contentment in your soon to be completed new home and lifestyle.
-blizz
__________________
2001 GMC 6500 Topkick, 22' box, dropped frame, designed to fit into a 9' garage door. 3126 CAT 6spd Man Lo-Pro 19.5's w/ 3.07 rear axle ratio
|
|
|
05-25-2010, 03:02 PM
|
#205
|
Senior Member
Join Date: Feb 2009
Location: St. Paul, MN
Posts: 1,819
|
Todd, I agree it does seem small. But, I think everybody has their own comfort level. In my camping miles I've met all sorts. Couples that have huge deisel pushers with 4 slides, families that have pop up trailers they have to all cram in to sleep, and everything in between. Forget about those tent people, they arent' real campers. I visit with and tour other peoples setups as well as offering my mobile home for them to check out. It always amazes me to see some of these people with teenie tiny campers and all the ingenuity they put into them. And they seem darn happy. I met a couple in Wyoming a couple years ago. They were "about half timers" to their camper. It was an old Ford van that they had built into a camper. Very compact indeed. They were very nice and seemed to fully enjoy their rig. I even wondered if maybe they wouldn't have enjoyed mine (but I had my '92 Allegro 32' gasser at that time). I guess it many ways, "size doesn't matter" hahahahaahah. Both of you guys amaze me with your creativness and skills.
Randy, I can just imagine you stomping on that piece of flooring in your driveway. I'd be the neighbor peering over the fence at you and just shaking my head. And then you'd go over and wrap a towel around yourself and poop in your gas toilet in the middle of the driveway. Hahahahaahaha.
__________________
'03 Freightliner FL112, 295" wheel base, with '03 United Specialties 26' living quarters, single screw, Cat C12 430 h/p 1650 torque, Eaton 10speed , 3.42 rear axle ratio
|
|
|
05-25-2010, 11:13 PM
|
#206
|
Senior Member
Join Date: Apr 2006
Posts: 625
|
....BOB86ZZ4 HAS DONE IT AGAIN.....NOW I HAVE THAT WORD PICTURE IN MY MIND ALL NITE WHILE TRYING TO SLEEP.....geofkaye and the Rivercity Group...
|
|
|
05-26-2010, 06:46 AM
|
#207
|
Senior Member
Join Date: Jun 2008
Location: West Chester, Ohio
Posts: 483
|
Yeah, thanks bob
__________________
Doc Weaver '98 Freightliner FL60 pseudo toy hauler
|
|
|
05-26-2010, 07:33 AM
|
#208
|
Senior Member
Join Date: Feb 2009
Location: St. Paul, MN
Posts: 1,819
|
You're welcome.
__________________
'03 Freightliner FL112, 295" wheel base, with '03 United Specialties 26' living quarters, single screw, Cat C12 430 h/p 1650 torque, Eaton 10speed , 3.42 rear axle ratio
|
|
|
05-26-2010, 09:31 AM
|
#209
|
Senior Member
Join Date: Dec 2002
Location: Hanford,CA,USofA
Posts: 786
|
Ohhh yeah, Bob, you are truly the "Master of Mental Imagery"!
I'm w/Geof on this one........;-)
Gary
|
|
|
05-26-2010, 10:57 AM
|
#210
|
Senior Member
Join Date: Apr 2009
Posts: 212
|
Blizz, Thanks for your kind words. You have a valid point, several actually. I have built a number of custom vehicles in my day. See the new added pictures under Keyword “Stealth”. (Apologies for hijacking my own thread…) I could never get my money back on any of these, which is probably why I still own all of them. I am amazed how some people can put blood and sweat into something for years and just sell it. That would be like selling my kids. Also, like my kids, no one wants to buy. My toys are a bit to specialized (strange) for general consumption. Ironically, once I move into the Stealth camper I will have no room for any of them, and they will all have to go (not the kid).
As for space, or the lack thereof, I too am concerned. My favorite room in the house is the garage. I don’t know what I will do without a garage and all my tools. I will have to store them somewhere, or sell them, and that’s like selling my kids again… Perhaps in time I can find a small industrial space to rent. Then I will have my mobile bedroom, den and kitchen, and my fixed garage. It will have to be cheap though…. Like a tin shack in the desert or something…
Bob, you crack me up ;-) And just for the record, I never did wrap myself in a towel and poop in the driveway. That’s my story and I’m sticking to it….
|
|
|
05-26-2010, 12:01 PM
|
#211
|
Senior Member
Join Date: Feb 2009
Location: St. Paul, MN
Posts: 1,819
|
I bought a storage condominium for my truck and junk. Owning is better than renting. Not cheap tho, I'll be paying for a long time on it.
__________________
'03 Freightliner FL112, 295" wheel base, with '03 United Specialties 26' living quarters, single screw, Cat C12 430 h/p 1650 torque, Eaton 10speed , 3.42 rear axle ratio
|
|
|
05-26-2010, 12:36 PM
|
#212
|
Senior Member
Join Date: Mar 2008
Location: West Fargo ND
Posts: 300
|
I was thinking after I typed that last post that maybe down the road if you felt you needed more room, a enclosed car trailer, insulated and carpeted with a A/C unit on the roof might make a nice companion stealth wagon. the way contractors all pull trailers now, nobody would notice.
You could put a comfy couch and big TV in it, with a zip up screen on the ramp door. Then you could have bicycles and other things that you and your son could play with or explore the country with. Maybe even a cheap old golf kart or scooter to run to the corner store with. The front could have a workbench and space for all your tools, thus eliminating the need for the garage.
Think about all that additional roof space for solar panels when the come down in price again.
That way we could follow another one of your very well documented builds!
-blizz
__________________
2001 GMC 6500 Topkick, 22' box, dropped frame, designed to fit into a 9' garage door. 3126 CAT 6spd Man Lo-Pro 19.5's w/ 3.07 rear axle ratio
|
|
|
05-26-2010, 03:37 PM
|
#213
|
Senior Member
Join Date: Feb 2009
Location: St. Paul, MN
Posts: 1,819
|
Wow, that's a great idea. Wear does he come up with this stuff?!
__________________
'03 Freightliner FL112, 295" wheel base, with '03 United Specialties 26' living quarters, single screw, Cat C12 430 h/p 1650 torque, Eaton 10speed , 3.42 rear axle ratio
|
|
|
05-26-2010, 06:55 PM
|
#214
|
Senior Member
Join Date: Feb 2006
Location: OKC, Ok.
Posts: 109
|
Actually, I built one from an 8 X 22' enclosed with ramp door.
I insulated the walls & roof, wired it for 110V AC with 30 amp RV service, 12V lights, installed an 18" awning, checkerboard tile flooring, Velcro'd in a screen rear door opening & side door. It makes a nice weekend camper for me & the motorcycle,...just set up a cot, throw in a small refrig & coffeemaker and take off.
|
|
|
05-27-2010, 12:08 AM
|
#215
|
Senior Member
Join Date: Apr 2006
Posts: 625
|
Bob that is exactly what I do with my tractor trailer....everything is on wheels/casters and i pick what i want to use for the trip-move it in --Tye it down to the e-track and off I go....also the girlz can add their own stuff as needed [and not use mine]........I got 24 new beer boxes like the old kind for beer bottles and use then as they protect the contents-are cheap-painted then with enamel and the girls pack them with all their crapola.....I have a few small suitcases for toilet stuff and a make up case for the girlz -the rest is in plastic bags....looks like a bunch of hillbillies came to town-but we are comfortable-no matter what the weather and I really don;t care what others think anyway-I'm on vacation!....One of my girlz was/is a professional entertainer and I have learned about the way to pack and what to take and what not to....Arminda can do a month of carbret work and live out of a suitcase the size of a 2 drawer file cabinet with room to spare.....I originally thought I'd need a trailer just for her stuff..and her daughters toys[9 mo old]....they take up less space than anyone else does....who am I to complain?.....geofkaye and the Rivercity Girls......
|
|
|
05-27-2010, 01:11 PM
|
#216
|
Senior Member
Join Date: Apr 2009
Posts: 212
|
My friends keep asking me where I am going to go with my Stealth Camper once it is done. Well this is one very good example...
|
|
|
05-30-2010, 07:48 PM
|
#217
|
Senior Member
Join Date: Apr 2009
Posts: 212
|
Propane Appliances Installed and Tested
This Memorial Day weekend I fully installed all of my propane gas appliances, tested them, and then removed them again. It seemed a shame to pull them back out, but I didn’t want them getting damaged when I installed the cabinet walls around them.
The Platinum Cat Heater was the easiest. It had already been installed and partly tested before the walls were closed. This time it was fully mounted to the wall and the thermostat was wired through the pre-installed conduit. I also added the foam weather strip around the bottom where I hope it will mostly draw filtered combustion air. I say mostly because it is not a closed system where I can force the issue. All I can do is give it a proximal inlet and hope that it mostly draws in cold outside air rather than using the warm inside air to make heat.
The range was next. I found my gas inlet hole in the floor was off by about 1/2 inch so it had to be enlarged in the right direction. I also found that I could have better placed my AC plug about an inch to the left, but I was able to trim the cover plate to accommodate. It doesn’t really need a cover plate at all since it is entirely behind the range when installed.
My original plan to bracket the range feet and hold them to the floor fell through when I realized that the rear range leveling feet are made of plastic. I don’t think they would be strong enough for my needs. I ended up making a rear fascia plate out of 1/16” aluminum that bolts to the back of the range using the existing screws. It then screws to the wall with 7 each #8 self tapping screws. I then removed the screw down front leveling legs and replaced them with 2 each 1/4” lag bolts using nuts and fender washers to space them up off the floor. With the front-bottom, and rear-top both secured the range isn’t going anywhere. I yanked on it good and hard and couldn’t budge it.
The range actually sits on 8 legs for distributed support. It has 4 “shipping legs” which are domed structures formed into the bottom sheet metal. They are nice and strong by virtue of their shape, and they also slide easily over flooring or carpet. I then screwed down the plastic rear leveling legs to provide some extra support, but only to take some of the load off the shipping legs. The front legs (lag bolts) also have spacers and fender washers to take some of the load off the front shipping legs.
It’s entirely a hard mount system and not intended to give or otherwise absorb bumps. I thought about using rubber pads or other shock mount techniques but to properly design such a system and have it really work is a sophisticated task. I was also worried about the gas lines having to move as the range moved which could potentially cause cracks and gas leaks. Ultimately I decided that the truck suspension will have to do its job to absorb the bumps and that everything inside will be locked down hard.
My remaining concern about the range is that it was not designed for RV use. The grates, and burner caps in particular are not locked down. I would not be surprised to see the top of my range all over the place after a rough ride. I may have to look into using some silicon glue to lock things down, hopefully in a way that allows me to take things apart for cleaning. That problem remains to be seen, and if necessary solved.
The toilet was my biggest concern, but it went in without much difficulty. The alignment of the flue pipe was not perfect. It’s off about 1/2” from top to bottom, but you would have to look carefully to notice.
I added a bracket to support the internal propane regulator. I can’t believe it didn’t have one in the first place, but I guess it was never designed for RV use. I also added a couple of brackets from the outer fire box to the floor. I am really amazed that it was designed with this big heavy steel box, that must weigh at least 50 pounds, and it wasn’t bolted down anywhere. It was just sitting there on top of some Cellotex insulation. The auger casting, auger, and drive motor were at least bolted to the plastic housing. Now everything is bolted straight through to the floor with 4 each 1/4” lag bolts. Even that strikes me as a little marginal, but it is infinitely better than what I started with.
The flue pipe mount through the roof worked better than I had hoped for. Once I got everything cut to length it fit up in the ceiling clamp perfectly. I was very worried about the sequence of assembly and disassembly. It’s one thing to build something once and have it fit. It’s another thing to design it so it can be taken apart for service without having to take a whole bunch of other stuff apart as well. (Like removing half you car’s front end to replace a broken headlight.) I lucked out in that I can easily remove the flue pipe and then pull the top off the toilet for maintenance. I can also get full access to the back of the toilet including the gas line, electrical control box, and ash removal port from outside the truck. OK, so I made my own luck with good planning, but don’t get the idea that I see every eventuality, because I don’t, and sometimes I really screw up.
This was my first chance to fully test the toilet in an “indoor” setting and the results were mixed. I gave it a real test (no towel required). It ran through the cycle and the machinery worked as expected. There was some odor unrelated to the toilet. When stuff drops into a bowl of water it is immediately covered and that reduces the smell somewhat. An incinerating toilet doesn’t do that, so even before the machinery does anything there is more potential for odor.
I had already removed the built in water squirting system for bowl cleaning. It didn’t do much and was just for show anyway. Instead I had a squirt bottle with water and about 5% alcohol, which did a much better job.
I have never been a fan of toilet paper as it relates to any toilet. It’s better than nothing, but it is no where near as good as a stream of fresh clean water, or in other words a bidet. I don’t have that option with an incinerating toilet, but the spray bottle is a limited substitute, which leaves toilet paper to help clean and dry things. I may refine the system, but it seems to be an acceptable and simple solution.
Once the toilet began the incineration cycle I noticed some smell inside the truck. Not the smell of raw sewage, but more like the smell of an oven after some food as spilled over and burned inside. It wasn’t much, and there was no visible smoke but I have to be honest and say that it wasn’t perfect either. It may be that I don’t have quite enough chimney to draw through the fire box even with the fan I added to pressurize the air inlet. For the moment it is acceptable to clear the air by running my overhead fan, but it’s not what I had hoped for.
A few hours later I went through the process of cleaning the ash. This would not normally be necessary for a month or two of use, but I wanted to test all maintenance activities as well. I was somewhat surprised to find that everything was not fully desiccated, let alone burnt. There was no smell, so I imagine it was all sterile, but I suspect that a single use is not a fair test. It may be that there is a cumulative incineration effect as the toilet is used and cycled. The toilet ends the incineration cycle when the exhaust gasses reach a certain temperature, meaning everything is desiccated. It seems a reasonable strategy, but some moisture may remain if it is not in the direct path of the flame, or if it is shielded inside a charred shell. I will have to withhold judgment pending further testing.
After all the testing, everything was removed, so I have an empty room again. The next time I install them it will be for good. Meanwhile I have only cabinets and furniture to build. There are lots of details to be worked out though. I still have a year of evenings and weekends to meet my original schedule.
The only remaining major appliance to install is the refrigerator. That is mostly a matter of building the structure around it as it does not sit directly on the floor. The connection to 12V power is almost trivial.
The next step is building the bunk beds. Everything will be built in place, so there is no more install and remove. What goes in stays in, so it will finally start to look like the finished product. The only remaining big ticket items are the counter tops and I still haven’t decided what materials to use. Beyond that there will be a fair amount of plywood for cabinet walls and shelves. There will also be the kitchen sink, and a long list of hinges, fittings, paint, and other small items. From here on out it’s much less about materials and mostly about labor, lots and lots of labor.
Several new photos have been added, so enjoy.
To be continued….
|
|
|
05-30-2010, 09:13 PM
|
#218
|
Senior Member
Join Date: Feb 2009
Location: St. Paul, MN
Posts: 1,819
|
This is great news. You're really moving now. Hay, for that stove top, what about making some sort of hard cover for it? My stove is set in below the counter and there is a board that fits in to completely cover it:
I thought they build those covers for the stoves to help cut down on the rattling noise while going down the road. But I would think it might work to hold everything in place on your stove top wouldn't it?
__________________
'03 Freightliner FL112, 295" wheel base, with '03 United Specialties 26' living quarters, single screw, Cat C12 430 h/p 1650 torque, Eaton 10speed , 3.42 rear axle ratio
|
|
|
06-01-2010, 08:09 PM
|
#219
|
Senior Member
Join Date: Apr 2009
Posts: 212
|
Bunk Bed Questions
I thought I would share some real time thoughts and ask for inputs on bunk bed design.
I have a rough plan, but as I approach a particular sub-project like bunk bed installation, I like to think through the design in more detail, and try to avoid creating problems for myself. I am at that point now on the bunk bed design. I am solid on the concept of using bunk beds, not drop down beds, fold up beds or any sort of convertible bed. I want the beds to be available for use on a moments notice, and I need 2 of them.
I have a limited ceiling height, 73” or 6’1” which is fine for me since I am only 5’9” and my son is 5’10’ or possibly 5’11” when he stands tall (which he rarely does).
I have mostly been thinking about the ergonomics of the bed, how it is used, and what is acceptable in terms of comfort. For example, it would be nice to be able to sit up straight when in bed, if for no other reason than to avoid smacking your head if you forget where you are and sit up quickly. It’s also nice to be able to sit up to take a drink, and sometimes when reading or watching TV to be able shift positions and sit upright for a little while. Given the limited ceiling height, that implies that the bottom bunk needs to be near the floor, but placing the mattress directly on the floor is a little awkward when getting out of bed, so the question arises, what is the lowest bottom bunk height that is acceptable?
Beyond sitting in the bed, there is the issue of sitting on the edge of the bed. That usually involves leaning forward and can be done comfortably (for a limited period of time) with your head outside of the sleeping area, meaning the upper bunk can be as low as just above your shoulders. Even if you want the upper bunk to be higher to allow for sitting in the bed, it allows for the possibility of a valance which can sit in front of a curtain rod to provide some privacy in the sleeping area. On the other hand, you still need to be able to lean back to lie down and you have to duck under the valance. Since the pivot point is your butt, which is about 8” inside the mattress edge, you need less clearance at the valance than under the rest of the bed to complete the maneuver. You can also lean sideways and back, which takes less vertical space, but requires more horizontal space.
In order to make sure my design wasn’t going to have me cracking my head on a daily basis I mocked up an entry frame on one of my existing beds. I was also able to mock up a partial ceiling to represent the upper bunk and get a feel for the head clearance as well.
It turns out that having the bed base (under the mattress) at 12” (above the floor) is a comfortably low height for the lower bunk bed, but I decided to “stretch it” just a bit to 8” in order to gain an additional inch of head clearance when sitting in the bed. My sitting head room of 31” above the bed base is marginally acceptable. All of this assumes a 6” thick foam mattress. I can’t sit bolt upright but I can sit comfortably upright.
The sit and roll back maneuver is no problem even with a 2” valance. You just duck your head as you roll back. Rolling back and sideways provides even more room, as there is no practical problem with the entry way width. Sitting on the edge of the (lower) bed is no problem at all except that the 8” bed base is a little low. It makes standing up a little more difficult, but it is not a problem, at least not at my current age and physical condition.
I ultimately decided that a valance to cover a curtain rod is unnecessary. Likewise a curtain rod is unnecessary. The “curtain rod” can be nothing more than a piece of bungee that stretches across and hooks on the far side of the opening. When not in use it can hook on the near side of the opening. The cloth curtain would have a tube sewn in to go over the bungee and would “scrunch” when the bungee is not stretched. Some light will get in at the upper edge but I don’t think that will matter. If I ultimately don’t like it, I can change it since it is not structural.
Getting in and out of the upper bunk is a little harder to mock up, but it is a fairly low upper bunk so I think my son can figure it out. I am a little concerned that he will smack his head against the ceiling as he levers himself out with his arms. I also expect that there will be a loud thump when he hits the floor. Heaven help him if he steps on me in the lower bunk when getting in or out. From what I recall of bunk beds when I was a kid, getting into the upper bunk is no problem. You just step on the edge of the lower bunk and dive in, or if you are an exuberant teenager you just jump and dive in. The outer rail of the bunk beds will be 2” by 1/8” steel L channel so I don’t think it will break, or even bend much.
Making up the bed is a whole other list of issues. I am not at all worried about the bed being “pretty” but I don’t want to wake up and be fighting with a random tangle of sheets trying to avoid this or that sticking out and getting cold. Most beds are much easier to make if you can walk around them and get access from all sides, with the possible exception of the head of the bed. In my case the mattress will be trapped within walls on most sides, and the only place you can walk, or kneel, is at the entry way on one side. The only way to make the bed is to crawl on the bed which is a pain. I am working on ways to mitigate the problem though.
The bottom fitted sheet is no big problem as you can hook it over the two far corners of the mattress and then stretch it out as you back out of the bed. Hooking it over the two near (side) corners is a slight hassle, but you can lift the mattress corner and bend it to you, then lay it back down again. Simple foam mattresses are light (and surprisingly comfortable in my experience). The remaining sheets, blankets, comforters, etc. are more problematic. Tucking them under the mattress doesn’t work well as they are hard to get positioned properly and tend to pull out, especially with a light foam mattress.
I have come up with all kinds of ideas, including sewing the bedding together, partially fitted upper sheets, zipper bags, Velcro, etc. They all have issues of one sort or another that I don’t like. The one idea that I think might be worth a try involves “buttons”. The “buttons” would be ¾” washers mounted on a short ¼” standoff, and screwed into the wall about half way down between the mattress and the outer wall. There would be at least two buttons at the foot of the bed and 3 or more buttons along the far wall. The flat sheet, blanket, Comforter, etc, would all have matching button holes sewed into the outer edge.
To make the bed you start with the fitted sheet as per normal. Then you crawl in with the flat sheet, hook it on the buttons and then stretch it out as you back out. Do the same with the blanket, comforter, etc. for as many layers as you want. I am concerned that the sheets will tear at the button holes, so I would fold them double, or even triple before sewing in the button holes. It’s a bit of a pain to have the sheets customized but it’s a simple job for anyone with a modern sewing machine. I like that the bedding can all be separated and washed normally. I also like that you can easily fold it back, or lie on top of it as you may wish.
It remains to be seen how all this will work out but there is nothing irreversible about it so the risk is low.
I can’t possibly be the first person to tackle these issues, so what have you all seen or done along these lines?
|
|
|
06-02-2010, 09:46 AM
|
#220
|
Senior Member
Join Date: Feb 2009
Location: St. Paul, MN
Posts: 1,819
|
Sounds like you've got it pretty well figured out. What about a small (3 step or so?) folding ladder/step stool that you can stow next to it, or under the lower bed. Then snap it out when using the upper bunk. That way you can easily move it from side to side as needed for makeup duties of the bedding too.
I don't know how much full sit up is needed on that upper bed. My son (now 19 and at college for 3/4 the year) and I built a loft bed for his bedroom at home about 4 years ago. He doesn't have enough room to sit up in his. He wanted it that way so he has plenty of room underneath for his gaming area. He likes it that way and has said he doesn't need to sit up. He likes to read in bed and just props up on a couple of pillows for that.
__________________
__________________
'03 Freightliner FL112, 295" wheel base, with '03 United Specialties 26' living quarters, single screw, Cat C12 430 h/p 1650 torque, Eaton 10speed , 3.42 rear axle ratio
|
|
|
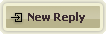 |
|
Posting Rules
|
You may not post new threads
You may not post replies
You may not post attachments
You may not edit your posts
HTML code is Off
|
|
|
|
» Recent Threads |
|
|
|
|
|
|
|
|
|
|
|
|
|