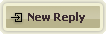 |
|
08-14-2009, 08:07 PM
|
#21
|
Senior Member
Join Date: Apr 2006
Posts: 625
|
....AH!..... the price should be $560.00 + any delivery/shipping fee......geofkaye
__________________
|
|
|
08-14-2009, 08:12 PM
|
#22
|
Senior Member
Join Date: Feb 2009
Location: St. Paul, MN
Posts: 1,819
|
Sounds good. I hope you've been taking lots of pictures along the way. How 'bout setting up a photobucket album or something for us to see?
__________________
__________________
'03 Freightliner FL112, 295" wheel base, with '03 United Specialties 26' living quarters, single screw, Cat C12 430 h/p 1650 torque, Eaton 10speed , 3.42 rear axle ratio
|
|
|
08-14-2009, 08:13 PM
|
#23
|
Senior Member
Join Date: Apr 2006
Posts: 625
|
...another issue....glob the sealer on the inside edge of the opening and install the A/C when still sticky ....make the bottom of the seal a gasket and leave the top of the seal loose-just reverse of the factory install....you won't a have any leaks and if necessary you can seal the unite from the inside with whatever you are using for caulk-smoothing it with your finger in a latex glove/or taped with duct tape and removable later without leaving the "black finger"....which is just like "stink finger" only it doesn't wash off with water....geofkaye
|
|
|
08-15-2009, 04:47 PM
|
#24
|
Senior Member
Join Date: Apr 2009
Posts: 212
|
Geofkaye,
Actually I paid $580 for the upper unit, and another $80 for the inside grill portion, and I picked it up myself from the local RV Store. I probably paid too much, but like I said before, I am a terrible negotiator.
I have been taking pictures along the way and I suppose I will have to find a way to make them accessable. I haven't taken the time to figure out how to do that yet.
|
|
|
08-15-2009, 09:30 PM
|
#25
|
Senior Member
Join Date: Apr 2009
Posts: 212
|
Some pictures are now available under keyword "stealth" or "Ran D. St. Clair".
|
|
|
08-15-2009, 09:51 PM
|
#26
|
Senior Member
Join Date: Apr 2006
Posts: 625
|
saw pix!...wish you said it was a Senco truck....I'm very familiar with the company-it is located less that a mile from my home-just outside of Newtown....anyway what you have is a on site/sales van. They are used for servicing/repairs and new equipment being sold to the contractor....low miles-lots of idle time and never hauled much weight to speak of.....you have what is called a cream puff. Most of the service unites are now obsolete and being taken out of service as the market has changed...geofkaye
|
|
|
08-16-2009, 08:46 AM
|
#27
|
Senior Member
Join Date: Feb 2009
Location: St. Paul, MN
Posts: 1,819
|
Where are the pic's?
__________________
'03 Freightliner FL112, 295" wheel base, with '03 United Specialties 26' living quarters, single screw, Cat C12 430 h/p 1650 torque, Eaton 10speed , 3.42 rear axle ratio
|
|
|
08-16-2009, 09:54 AM
|
#28
|
Senior Member
Join Date: Apr 2009
Posts: 212
|
Hauling AC…
So much for not being in a hurry to spend money…. I purchased my air conditioner (Coleman Polar Cub, 9200 BTU, 9A), and generator (Honda EU2000i (17A maximum, 13.3A continuous). Naturally I was eager to put them together and see what would happen. Unfortunately the RV place where I bought them was booked up on installations for almost 2 weeks, so I decided to install the AC myself. The only part I was at all concerned about was getting it up on top of the truck.
The AC unit came packaged on its own small pallet, with a cardboard box cover including reinforcing cardboard at the corners, presumably so they could be stacked. The pallet had two fairly sturdy self tapping screws installed with plastic bushings that fit into holes in the sheet metal on the bottom of the unit. They did not hold the unit down onto the pallet, but they did act to keep it from sliding around on the pallet. After removing the cardboard top, I put several loops of rope over the unit and under the pallet to make sure they would stay together. I also reinforced the front cross piece on the pallet with a few sheet rock screws. I didn’t want the staples pulling apart for what was to happen next. I then tilted the pallet and the AC unit 90 degrees nose up and shook it around a bit to make sure it was going to stay together.
A friend of mine and I set up a single ladder up against the back of the truck at a comfortable climbing angle, and also so the top of the ladder extended past the top of the truck by only a few inches. We tied a stout rope to the front cross brace on the pallet and threw the free end up on top of the truck. We set the pallet on top of the ladder, which meant it was sitting nose up about 80 degrees, roughly balanced on the back corner of the pallet. I then climbed up on top of the truck and started pulling it up with the rope. Meanwhile my buddy was pushing and guiding it up the face of the ladder from below. The unit weighs about 90 pounds, but it was easy. In less than a minute it was at the top of the ladder where we gently laid it flat on top of the roof. I might have been able to do it entirely by myself, but having two people made it much easier and safer.
Once on top of the truck it was just a matter of shifting it into place and bolting it down. Just 4 bolts between a metal bracket that mounts on the ceiling opening and the AC unit above and it was weather tight. The previous work I had done to make the 14.5” x 14.5” opening and reinforce it with 2x6 rafters worked perfectly. I won’t bore you with the rest of the installation. The instruction manual was adequate, and it was pretty simple. Some of the self tapping screws didn’t want to go into the sheet metal, but drilling the holes out a touch fixed it right up.
I bought a heavy duty extension cord, 3 wire, rated at 15A, cut off the female end, and temporarily wired it into the unit for initial testing. The generator needed oil and gas, but it took longer to read the owners manual than it did to get it running.
I don’t have my clamp on AC and DC Ammeter yet, so I don’t have hard figures but I did learn a few things. The generator seemed to handle the air conditioner just fine, at least on a cool day, which is hardly a difficult test. There was also no other load on the generator, like a battery charger, so it was far from a worst case scenario. I was able to run the generator in economy mode and it was able to handle the compressor turning on without stalling the generator. When the compressor was running in high cool mode, switching the generator from regular mode to economy mode allowed it to slow down considerably, implying that it was not working hard to keep up with the steady state requirements of the air conditioner.
I was forced to run the generator in free air on the ground next to the truck. My generator bay needs to have a hole cut in it to allow exhaust air to exit. It has plenty of holes in it now, just not in the right places. As a result the generator was breathing some of its own exhaust and probably would have overheated if given the chance.
I don’t recommend this, but I wanted to see what would happen if the air conditioner was dealing with a really hot day, so I put the vinyl cover on it. Ok, true confession, I forgot that the AC cover was already up there. In about 5 minutes the back pressure built up in the compressor and the generator started surging. Shortly thereafter the red light on the generator came on and it stopped providing power. The engine was still running, and the circuit breaker never popped, so it appears that the internal electronic circuitry cut the power to the exciter winding. No permanent damage was done (as far as I know). I reset the generator by stopping and restarting it, and of course I removed the AC cover. It may have been stupid (OK it was stupid) but I consider it a valuable learning experience. I now know what an unhappy generator sounds like, even before the red light comes on and it cuts the power.
Unfortunately it was a completely uncontrolled experiment so I don’t know if it simulated a 90 degree day or a 150 degree day. I do know, however that the generator is the weak link in the chain, and that it will protect itself if pushed too far. The manual warns, however, that I should not rely on it to protect itself in this way, as this sort of abuse will shorten its life.
To be continued...
|
|
|
08-16-2009, 10:02 AM
|
#29
|
Senior Member
Join Date: Mar 2008
Location: West Fargo ND
Posts: 300
|
Quote:
Originally posted by Bob86ZZ4:
Where are the pic's?
|
link to photo section w/ pictures
Stealth RV
blizz
__________________
2001 GMC 6500 Topkick, 22' box, dropped frame, designed to fit into a 9' garage door. 3126 CAT 6spd Man Lo-Pro 19.5's w/ 3.07 rear axle ratio
|
|
|
08-16-2009, 10:23 PM
|
#30
|
Senior Member
Join Date: Feb 2009
Location: St. Paul, MN
Posts: 1,819
|
Thanks for the picture link, Todd.
__________________
'03 Freightliner FL112, 295" wheel base, with '03 United Specialties 26' living quarters, single screw, Cat C12 430 h/p 1650 torque, Eaton 10speed , 3.42 rear axle ratio
|
|
|
08-18-2009, 09:19 PM
|
#31
|
Senior Member
Join Date: Apr 2009
Posts: 212
|
I was framed I tell ya…
Now that I have the ceiling framed out and the roof weather tight, it is time to start framing out the interior walls. The general idea is to put 2x4’s (Actually 1.5”x3.5”) in the corners and 2x2 (Actually 1.5”x1.5”) studs, or verticals, on the inside of the FRP on 16” centers. I won’t bore you with every detail (any more than I already have) but even such a simple idea has its challenges.
For one thing, it means building a square cornered box inside of a sometimes round cornered or otherwise irregular box. I have done a lot of “carving” with my skill saw. That’s where you drag the blade sideways across the surface of the wood chewing it down to whatever shape you need. Pretty much every stick goes back and forth between the back of the truck and the garage 3 to 10 times being carved and fitted to just the right shape. I have spent an entire evening after work on one piece of wood more than once.
Everything is screwed and glued. I honestly don’t know how well “Liquid Nails” will stick to FRP, but all the studs have a solid bead of glue along with sheet rock screws every 12” or so holding them up. The FRP on the outer walls is roughly 5/8” thick so I am using 2” long sheet rock screws with a fine thread of the sort that are often used to punch into sheet metal studs. Clearance holes are pre drilled and countersunk into the studs to make sure they are pulled firmly to the outer wall.
I use a cordless electric drill with a screwdriver bit to punch in the sheet rock screws very carefully. Too much torque and they will either strip out the hole in the FRP, or worse yet, pull the head into the soft stud and punch through to the outside. I really don’t want to break the outer skin of the FRP and encourage delamination due to moisture incursion.
The exact placement of the studs varies due to feature locations, but every seam for the 4’x8’ plywood inner walls has to be supported. The plan is to use ½” smooth finish plywood and just paint it with latex paint. I know that’s not very fancy, but it’s functional. Joints will be caulked and then possibly brought to level with a little non-shrink spackle. I don’t plan to do much with moldings unless it is just convenient to cover up a gap or a crack of some sort. I don’t see much point in doing more because almost every inner wall is going to be covered with storage cabinets or shelves of some sort.
The floor plan is still slightly in flux, but I decided in general not to try to position the studs in exact locations to support features or cabinets. The ½” plywood inner walls should be strong enough to support whatever is necessary, especially if everything is designed to be supported from the floor up. In other words, overhead cabinets won’t be just hung on the wall. They will have at least partial sides, like a bookcase, that help to provide support from the floor to the ceiling.
In order to nail the floor plan down to the last inch, I need to lay hands on all of the major appliances. That means toilet, range, refrigerator, etc. This is where thousands of dollars will be spent. It’s also where I will most likely make my most costly mistakes.
Up until this point I have been writing mostly about what I already did. Now I am starting to get into what I am planning to do, which means I will have to tell you about changes in plans as they occur. I am also reaching a point where I have to start thinking much farther ahead. I can easily paint myself into a corner and cause myself a lot of grief at this point. Progress is slowing way down while I try to imagine everything that needs to go into the walls before they are closed up. That is driving a lot of design issues with the electrical system, propane system, air conditioning and circulation and filtration system, etc. It’s like I need to know exactly how all this is going to turn out, and I guarantee you, I am not that smart.
On the other hand, this is also where it gets interesting. There are sooo many design tradeoff’s to consider. Every piece of this puzzle affects every other piece, and the more efficient everything has to be, the less room there is for overkill.
To be continued…
|
|
|
08-19-2009, 07:44 AM
|
#32
|
Senior Member
Join Date: Apr 2006
Posts: 625
|
...hold up...Liquid Nail will probably not stick to FRP call/search 3M and get their view of what you are wanting to do....I'm thinking POLYSEAMSEAL but I could be incorrect....it has to stay flexible and never harden....also a 2 part epoxy might be better....scuff the surface to be glued.....it also needs to be pristine. Run electric up through floor with SO chord etc...ceiling only needs to be 2.5 inches thick if you use foam board like SuperMaxx/R-MAXX or one of the polyisocynates with aluminum foil on each side....geofkaye
|
|
|
08-19-2009, 06:54 PM
|
#33
|
Senior Member
Join Date: Apr 2009
Posts: 212
|
Geofkaye,
I think you have a valid point about the liquid nails and FRP. I should have done some destructive testing before I got so far along. At this point the deed is mostly done, but I could get some Polyseamseal and run a bead up and down the sides of the studs to help out the liquid nails. I also meant to rough up the walls with my disk sander before gluing but got in a hurry (excuses, excuses). For the benefit of others, here is the web site for Polyseamseal.
http://www.polyseamseal.com/allpurpose.shtml
I am sure a 2 part epoxy would have been very strong, but given the slow process for putting up the individual studs it would have been onerous. Fortunately, once the plywood goes up it will effectively lock everything in place. The inner walls can't peel away from the outer walls because the floor and ceiling will get in the way.
Electrical will run up through the floor, but once inside be distributed via conduit in the walls and ceiling. It might be easier to run things under the floor, but I don't like the idea of exposed wires running around under there. I would have to put conduit under and around the frame bits, which I may have to do to some extent anyway, but mostly I want to run from the underbed boxes up through the floor and then remain in the protected environment inside the box.
I am surprised to hear you say I only need 2.5" insulation in the ceiling. I had heard a somewhat vague unscientific statement that 80% (or something like that) of heat loss was through the ceiling. Therefore I had assumed that I wanted considerably more insulation in the ceiling than the walls. At this point the rafters are already in place so I will just fill it with R-Maxx to 5 1/2" thick at the most, and less in places where the shape of the roof or conduit dictates. If I spend a little more than I needed to on insulation then it will probably be one of my smaller mistakes on this project.
Speaking of insulation, I am wondering what is your opinion of using multiple layers with aluminum foil on the layers. In the walls for example, I was thinking to use 3 layers of 1/2" R-MAXX with the foil to the inside. I don't have a good handle on the exact physics of how multiple layers of foil would relate to the reflection, absorbtion, and re-radiation of IR energy through the layers, but my intuition suggests it would be more effective than just one layer, especially if the foil on that one layer is in direct contact with the plywood of the inner walls. Once again, this is an area where I am willing to spend money.
Beyond the R-MAXX I will be using the can foam to fill cracks and lock everything into place. That and I figure a plastic vaper barrier just before I throw up the inner plywood. I am hoping that this will be one very well insulated structure, and so well sealed that I will have to pay special attention to venting to keep from dying for lack of air.
Thanks for your input. I am listening...
|
|
|
08-19-2009, 07:04 PM
|
#34
|
Senior Member
Join Date: Apr 2009
Posts: 212
|
Warning – Discussion of electrical systems can be dangerous (To your wallet)
Lets talk about the electrical systems. This is theory and philosophy mind you, since I haven’t actually built it yet. I am an electronics engineer, so I at least know ohms law, but I am not an electrician, though I do at least know the difference between ground, neutral, and hot. I will try not to lead anyone astray with mis-information. I have read “Managing 12 Volts” by Harold Barre and I recommend the book.
My project requires that I be able to operate independent of the grid (shore power) indefinitely, though I may have access to the grid at times. I realize that is very different from what many of you are doing, so it drives a different approach. I also have a bent towards efficiency. It’s not some green save the whales thing, it’s just my nature.
It seems to me that there are four kinds of electrical power that I need to handle and distribute:
1. 12V DC (Direct Current) related to the truck starting battery
2. 12V DC related to the house batteries.
3. 110V AC (Alternating Current) from the on board generator, or shore power if available.
4. 110V AC derived from the house batteries via an inverter.
I realize that many of you will have a shorter list. You may not feel the need for an inverter, or even batteries beyond the starting battery. You may only have 110V AC (AKA 115V or 120V AC) and not even use 12V DC beyond the cigarette lighter in the cab. Certainly you probably only have AC wiring in your fixed base home.
You might wonder why I make a distinction between the 12V starting battery and the 12V house batteries. Some really simple systems just use the starting battery for everything, or use diodes, relays, solenoids, or manual switches to connect them together at one time or another. All of those might be a reasonable option depending on the situation, but I think it is often a bad idea, and I don’t plan to do it.
The 12V starter battery and the 12V deep cycle house batteries are fundamentally two different types of batteries. They may both be 12V lead acid batteries and they may look similar, but they are not. The starter battery has porous lead plates for maximum surface area and maximum starting current. It should never be deeply discharged, and while one or two short term deep discharges might not kill it outright, each one takes a toll and it will soon be useless. A deep cycle battery has thicker stronger solid lead plates. Since the plates have less surface area it won’t be able to deliver as much short term current for the equivalent physical size. It can be discharged and charged many more times, but it should still not be discharged below 50% of capacity and each deep discharge cycle still takes a toll that will eventually kill it.
I have to say that lead acid batteries in general are a very poor technology for house batteries. There are many far better technologies out there, and new technologies are being developed every day. For the time being though, lead acid batteries are the only cost effective solution. I expect that will change dramatically in the next 10 to 20 years as electric cars become more popular.
Every method for connecting the starter battery to the house batteries has potential problems.
Manual switches can be great, if you know when to turn them on and can remember to turn them off. I might consider one as an emergency option, but I know that when it comes to remembering things I am an idiot, so I wouldn’t want to rely on it all the time.
Diodes have a voltage drop, dissipate a lot of power and get hot, and send all of the energy from the alternator to the weaker (more discharged) battery. If the house batteries are weaker, they get all the juice, and the starter battery never gets charged. Keep doing this long enough and eventually the starter battery is just as discharged as the house batteries, which isn’t good for it. Of course, if you run the alternator long enough, eventually all the batteries will get fully charged and everything will be OK, assuming you have somehow compensated for the voltage drop of the diode. That might take a long time though because regular alternators are designed to charge very slowly and conservatively, especially as the battery gets closer to being fully charged. You could use an expensive high current alternator and a matching expensive 3 stage voltage regulator, and then adjust it to compensate for the diode drop, but even after all that, you better run the engine long enough to fully charge all the batteries. You could even hook the house batteries to an AC charger driven by shore power and never let them get discharged, but if you are going to do that you really don’t need house batteries at all.
You could use a continuous duty solenoid between the house battery and the starting battery, to connect them only when the engine/alternator is running. The problem here is that a discharged house battery will immediately suck up all the current from the alternator, and will even start pulling current out of the starting battery, drawing it down even faster than in the diode example above. The current surge when the solenoid turns on will be tremendous, so the wiring had better be able to take it. It’s very much like giving another car with a dead battery a jump. Do it once and it’s not a problem. Do it over and over again without giving your battery a chance to recover and you will need a jump yourself. Considering that your house batteries might have much more capacity than your starting battery, they can suck it dry and still be hungry for more.
One of the most sophisticated options for connecting the house batteries to the starter battery is a Battery Combiner or Electronic Feedback Relay. It uses solid state circuitry and the intelligence of a small computer to attempt to get around the problems with diodes, solenoids and manual switches. The general idea is that it monitors the voltage on all the batteries, which could include multiple banks of house batteries. If any one of them has a high voltage, indicating that it is being charged, then it connects all of them together so they all get charged. Unlike a diode, the voltage drops are minimal, but like a solenoid, the current surge can be very large when the batteries are first connected. They can also discharge the starting battery into the house batteries, just like with the solenoid. Battery combiners are also quite expensive.
All of these methods are being used, and there are probably many people out there that are happy with every one of them. For my purposes they are all not good enough. I might consider a manual switch just so I can use the house batteries to jump a dead starter battery though. In general I want my house batteries and starting batteries to be completely separate systems. I don’t want to compromise the reliability of the truck starting system. Besides, running my truck engine all day to keep my batteries charged would be terribly inefficient. It might be reasonable to charge the house batteries from the alternator on a long drive, which I can still do with a manual switch, if I can just remember to turn it off when I get there.
I could put a 2nd high current alternator on the truck, with a 3 stage voltage regulator, and charge the house batteries completely unrelated to the starter battery. I am sure it would work, but it would be expensive, and require mechanical modifications to the truck. I am too cheap for all that. Better to use a high efficiency generator, and a battery charger to keep the house batteries up to snuff.
Speaking of generators, I am told that the little Honda generators (or similar) are up to 3x more efficient than some of the larger gas or diesel gensets that are often used on luxury RV’s. Those big generators have many other nice features and may be the only good option for you, but not for me. I don’t need to run 2 air conditioning units and all the electrical what not’s for a family of 5. That brings up the question of what do I, or you, need?
I’ve done the math and it is amazing how cheap and convenient electricity is from the grid. You don’t fully realize that until you try and make your own, or worse yet, store enough to meet your needs in batteries. You have to pound yourself down to what you really really need if you want to live off of batteries for more than a day or two.
To be continued...
|
|
|
08-19-2009, 08:16 PM
|
#35
|
Senior Member
Join Date: Feb 2009
Location: St. Paul, MN
Posts: 1,819
|
I have two 12v deep cycle house batteries. I have 3 12v cranking batteries for the truck chassis. The cranking batteries also start the generator. I have a large rotary switch that allows me to use the house batteries for house 12v stuff. Or I can switch it to use the cranking batteries for the house stuff. Or I can set it to tie all 5 batteries together. I think this is the best system for you to use. The key here is that you can use your deep cycles without worrying about having cranking power. Then, when you start the engine for whatever just turn the switch to charge up all your batteries. Don't worry about remembering to set the switch. You'll remember. Otherwise if you don't have the switch how were you going to charge up the house batteries?
Now, I'd also advise you consider 4 or 6 6volt deep cycle golf cart batteries. My old class A motorhome had 4 x 6volt deep cycle golf cart batteries for the house power. You wire up two batteries in series and the other two in series, and then both pair in parrellel for a final voltage of 12v. This will give you tons of house power reliably. Then to top it all off put a couple large solar panels up top. My class A had three huge ones. It was great! Never a worry about house power with that coach. I would have liked to remove those solar panels and put them on my new coach if it wouldn't have been so much trouble. I left it all as it was and the buyer is very happy to have such a system. That coach also had an emergency relay that had a momentary contact switch I could push to use the house batts for cranking if for some reason the cranking batt was dead. I think that rig had a relay that engaged when the engine was running to tie all the house batts together and charge them from the alternator. It was a constant duty one, I know because it failed so I had to replace it for about $40. But, it was probably original equipment, 15 years old.
If you don't have something like this then every time you run your house batts down you'll have to start the generator or find shore power to charge them back up. Much better to be able to fill those house batts from the truck engine if you happened to be running that motor for some reason. If you don't have a need to start the truck then for sure just use the generator or shore power. But those solar panels are great, but expensive.
__________________
'03 Freightliner FL112, 295" wheel base, with '03 United Specialties 26' living quarters, single screw, Cat C12 430 h/p 1650 torque, Eaton 10speed , 3.42 rear axle ratio
|
|
|
08-19-2009, 09:37 PM
|
#36
|
Senior Member
Join Date: Apr 2006
Posts: 625
|
...IMHO:...A larger diesel generator is 120/220vac up to 100 amps [about $ 3500] and a smaller gasoline and/or propane generator [$1000] is 120vac also have a good battery charger [$150]that you plug into the small or large generator for 12vdc coach electricity/battery charging etc.......then you are covered all the way around charging the coach batteries/running in the nite to keep cool/warm-running 120/220 vac appliances anytime any place under any conditions and last but the most important your battery charger will charge the truck batteries/the house batteries and will run the 12vdc things very well....cheaper and more reliable... forget the transfer switches and any of that gizmo crap....use plugs and recepticals and there won't be any mistakes and that flash/jolt when you cross things won't happen. The unites will cover for each other-also cross over to take over electrical things under any circumstances....which is a miracle when things go badly these days.....geofkaye
|
|
|
08-20-2009, 09:26 AM
|
#37
|
Senior Member
Join Date: Jun 2008
Location: West Chester, Ohio
Posts: 483
|
question: What's wrong with tying all the batteries together?
I went as simple as I could. The only 12v units in my truck are the lights and water system pump. Everything else is 120v and run to a breaker box. So when I'm "camping", I either run the generator or plug into shore power. As far as the 12v systems, I start the truck to restore battery power every other day.
Doc Weaver
__________________
Doc Weaver '98 Freightliner FL60 pseudo toy hauler
|
|
|
08-20-2009, 03:43 PM
|
#38
|
Senior Member
Join Date: Apr 2009
Posts: 212
|
All, I’m glad to see you are still following along. I must confess, I am about 10 posts ahead of this thread. I could post them all at once, but that would kill all this good back and forth. I will get to some of your suggestions about batteries and what not soon. In the mean time, I am not ignoring you.
Bob86ZZ4, I am planning to have a switch to connect the house batteries and the starter batteries in parallel. Unlike a vacation RV I won’t be traveling all that much, so charging all the batteries by running the engine would mostly be a waste. Most of my short trips will barely put enough energy back into the starting battery to make up for what was lost starting the engine.
Solar panels are a big topic. I could cover the entire top of my truck with them and it still wouldn’t make a dent in my total energy needs. It would mostly be an expensive social statement. I think a small solar panel is a good idea for an occasional use RV as an easy way to keep the batteries topped off when not in use. I also think they have a place in a fixed point application where grid power is not available, like a remote cabin in the woods. The last I heard, it takes more energy to make a solar panel than it will generate during its entire life time of use. The engineer in me cringes at the false economy created by tax breaks and what not because it just makes no sense.
Geofkaye, I would love to have a large generator and a small one as well, but I don’t have room for the larger one, let alone both. I am with you on using plugs and receptacles with no transfer switch, as you will soon read.
Doc Weaver, “What's wrong with tying all the batteries together?” Nothing if it works for you. It sounds like your DC needs are small and your truck starting batteries large. The risk is that you could run your starting batteries down and not be able to start your truck. I have never tried to jump a large truck, but I am guessing my little subcompact would have a hard time of it. Beyond that, by drawing your starter batteries down even half way and then charging them back up again you are shortening their life somewhat. Perhaps you don’t do it that often so in the grand scheme of things it doesn’t matter very much.
More later...
|
|
|
08-20-2009, 07:36 PM
|
#39
|
Senior Member
Join Date: Apr 2009
Posts: 212
|
Evolution of Design
I started the electrical design with some preconceived notions about how it was going to work, but that’s not at all where I ended up. I could take you through the whole journey, but unless you are really into amps and amp hours the trip would probably put you to sleep. Let me try to condense it down and spend most of my time (your time), on where I ended up and why I went there.
My initial thought was that an air conditioner draws too much current to be powered from an inverter, or more to the point, from batteries. Therefore I resolved to plug the air conditioner directly into the generator, and then use the left over current from the generator to charge the batteries.
Another assumption was that I would end up using a more or less standard RV style Inverter – Charger – Transfer switch.
I also started by using a design philosophy that I got from “Managing 12V” by Harold Barre, that basically involves calculating your energy requirements for an entire day (or whatever time period you choose) and then providing enough battery capacity to meet your needs. No offence to Harold Barre, whose ideas are perfectly valid. But none of these things worked for me.
Lets start with plugging the air conditioner directly into the generator. I had been really struggling with the issue of how to deal with the highly variable load of the air conditioner. It’s well within the range of my generator when it is running, but the startup current whenever the compressor turns on can be really high, and it also varies with outside temperature. That and the fact that I just can’t accurately predict it based on the manufacturers data.
I really hate that there is all this leftover generator capacity that I can’t use because I never know when the air conditioner is going to need all of the available capacity, and possibly even more. The highly variable load could easily damage my generator over time, possibly shortening its life. It could also force me to buy a 2nd generator, for another $1,000 or so, and then I would have even more capacity that I can’t entirely count on.
Finally it hits me, there is another option. I know I said I never want to run the air conditioner off of the batteries, and I still don’t, but I might just want to run it off of the inverter. It goes something like this. I buy a 90A battery charger, and then connect the battery charger, and only the battery charger, to the output of the generator. The generator is rated at 13.3A continuous, so it should be able to drive the battery charger (13A) all day long.
The output of the battery charger is then connected to the input of a high power inverter which in turn drives the air conditioner and all of the various AC appliances. It also connects to the batteries of course.
At full running load in desert conditions (120F) the Air conditioner needs 1,260W. The maximum load for all the other AC appliances turned on all at once, including the microwave is 1,387W. Altogether that’s a total of 2,647W. As a practical matter it would probably never go above 2,500W. If I just promise to never run the microwave when the air conditioner is on it drops to 1,847W.
There are many battery chargers in the 90A range from $400 to $600. Some are more true multi-stage chargers and others are more like power supplies. Some are more ruggedized for mobile use and some tend to be more for fixed installations.
There are also many inverters available in this range from a few hundred dollars to around $1,000 depending on features. It might even be handy to use two smaller 1,500W inverters, that way the one that provides power to the air conditioner can be disconnected from the batteries when not in use, so it doesn’t constantly drain the batteries even when providing no power.
There are also battery chargers, inverters, and transfer switches all in one nice neat robust package, but I will get into why that doesn’t work later.
At 2,500W the current draw from the batteries would be about 241A. That’s a heck of a lot of current and would draw a 440Ah (Amp Hours) battery pack flat in under 2 hours. Since I would never want to draw the batteries below about 50% the holdup time is actually less than an hour.
As a practical matter I would not want to even pull that kind of a load from a 440Ah battery pack since it would exceed 25% of the Amp Hour rating (110A). Thanks to something called the Peukert Effect a lead acid battery being discharged in 4 hours or less has much less energy capacity than the nominal 20 hour rating. Put another way, if you draw too much current from the battery then a lot of energy gets wasted heating up the battery.
As a practical matter, I would never turn on the air conditioner, microwave, and everything else all at the same time. A more likely maximum current, and even this is on the high side is 15.5A AC which translates to about 158A DC. That’s still a lot, but it’s getting more reasonable.
If I start the generator first, before the air conditioner, the battery charger is ready and waiting to put out up to 90A. It might not put out the full current at first, but it would very quickly sense that the batteries are drawing down and begin to provide full current. 158A load, minus 90A from the charger leaves 68A to come from the battery. That is well within the 25% rule or 110A. At that rate the batteries would only last about 6 hours, but since I can only use 1/3 of their capacity it’s more like 2 hours. That sounds pretty bad, but this is a worst case instantaneous current calculation.
If I turn off all the computers, monitors, PlayStation3, etc. and just hang out and read a book in air conditioned comfort, I wont need any AC current except for the air conditioner. That’s about 1,200W on low cool, even at 120F outside. But wait, If I have done a half decent job with my insulation then the air conditioner compressor will only be on about half the time, or hopefully less. It takes about 137W to run the fan on low cool, so on average my air conditioner will be drawing 668W, or 6.1A AC, or 56A DC.
There’s probably another 5.5A of DC for the refrigerator and what not, for a total of less than 61A DC. That means my battery charger is actually putting 90A minus 61A, or about 29A back into my batteries. My son can fire up the PS3 (Which is a power hog) and we are pretty much breaking even. Now if the generator quits, I better turn off the air conditioner or get the generator started up again within an hour or so, but it’s not a panic.
The point of all this is that my generator is churning along at something like 90% of its capacity (depending on the choice of battery charger) and that load doesn’t vary when the air conditioner compressor comes on, or pretty much ever. It might reduce as the batteries approach full charge, but it never exceeds the maximum dictated by the charger. If the load on the generator does change, it will change slowly because the batteries can’t be charged or discharged very quickly. That means I can leave the generator in economy mode and it will happily do whatever it needs to do to feed the charger.
The downside is cost. The battery charger is close to what I would have wanted anyway, but the inverter has to roughly double in capacity. That’s another $200 to $500 depending on the specific choices. There are a few other odds and ends, like heavier DC cables, but it’s probably in the noise. Within reason, I will spend money to reduce risk, and I like this tradeoff.
Another downside is efficiency. Converting AC-DC-AC drops my efficiency to about 85% (.90 x .95). If the energy goes into the battery and then comes back out again it’s more like 73% (12 / 14 x .90 x .95). Throwing away over ¼ of the precious energy from my generator sucks, but that’s life.
When shore power is available I just connect it to the battery charger and directly to the air conditioner. That way the batteries are sure to be fully charged at all times. One side benefit of converting from AC-DC-AC is that I have lots of isolation from power surges or what not.
I would still probably buy a 2nd generator though. I wouldn’t need it. It would strictly be a back up. There I go spending money to reduce risk again. Now I can start worrying about the reliability of all these components. There is always something to worry about.
Some battery chargers I found on line that might fill the bill include:
Iota Smart Battery Charger / Converter, 90 amps, 12V, Model #:CHG-DLS-90, Maximum AC Current @108Vac: 13 amps, $369.
http://www.theinverterstore.co...hp?model=chg-dls-90#
In order to make it a 3 stage battery charger and not just a DC Power supply you also need the Iota Smart Controller for DLS Battery Chargers, Model #:CHG-IQ-4, $29.00. The price is very tempting, but I worry that it lacks temperature compensation, and the 13.6V maximum output voltage would likely charge the batteries very slowly as they near full charge. Still, it looks like a worthy option.
If I want a little more safety margin I can use the 80 AMP 12V Battery Charger, by Samlex SEC-1280A, $609.
http://www.donrowe.com/battery...arger_12v_2bank.html
The Samlex appears to be more of a true 3 stage battery charger with temperature compensation and a higher boost voltage (14.4V), which is probably why it is more expensive. The maximum AC input current isn’t specified, but based on the lower output current it is probably about 11A.
To be continued…
|
|
|
08-20-2009, 07:59 PM
|
#40
|
Senior Member
Join Date: Apr 2006
Posts: 625
|
.....OK TWO SMALL GENERATORS AND IT IS A WASH...PRIMARY AND BACKUP AND ONLY ABOUT $2K NEW AND ABOUT $1400 USED....I could find cheaper unites from a HONDA dealer this time of the year should I have a lot of time to go face to face with some cash.....so maybe I could get 2 for the price of one.....or even 2 new and 1 used for $1400 out the door cash.....there are a lot of generators just laying around that were purchased during the big storm last year and are on the market now for cash......Craig'sList has about 4 currently tonight and there are a bunch of off shore unites available most about 4-5000 watt unites for around $4-500 and with those-cash is still king!....geofkaye
__________________
|
|
|
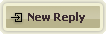 |
|
Posting Rules
|
You may not post new threads
You may not post replies
You may not post attachments
You may not edit your posts
HTML code is Off
|
|
|
|
» Recent Threads |
|
|
|
|
|
|
|
|
|
|
|
|
|