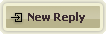 |
|
10-01-2013, 08:31 AM
|
#1
|
Senior Member
Join Date: Apr 2012
Location: Elyria
Posts: 108
|
Freightliner M2 Build
First, thanks for the website and all the ideas. We would like to show our build as a sort of repayment. "We" are : my son Robert, 29 yrs old, sheet metal worker and our main welder. My son Ryan 26 yrs old who is a machinist. As for me, I just retired from 36 years as lab tech/production supervisor/superintendent at The chemical company. We have been drag racing and building our own dragsters since Robert was 8. So besides their full time jobs(with OT), drag racing on weekends, drag racing side jobs, and taking care of their homes, they are pretty booked. I try to organize everything during the day to make the most of their time in the evenings. So let the build begin.
__________________
|
|
|
10-01-2013, 08:39 AM
|
#2
|
Senior Member
Join Date: Apr 2012
Location: Elyria
Posts: 108
|
8/15/13 - Day 1
Main rails are 3 x 5's with the rest of the floor 2 x 2's.
__________________
|
|
|
10-01-2013, 08:44 AM
|
#3
|
Senior Member
Join Date: Apr 2012
Location: Elyria
Posts: 108
|
8/16/13 - Day 2
Floor Complete
|
|
|
10-01-2013, 08:56 AM
|
#4
|
Senior Member
Join Date: Apr 2012
Location: Elyria
Posts: 108
|
8/23/13 - Day 9
Took 4 of us to lift and slide the floor on truck. We used oak boards between the truck frame and floor. Made our own u bolts with all-thread and 4 side plates to keep it all in alignment. Hopefully we are not too rigid.
|
|
|
10-01-2013, 09:02 AM
|
#5
|
Senior Member
Join Date: Apr 2012
Location: Elyria
Posts: 108
|
9/2/13 - Day 19
Wall one complete. Its made out of 1.5 x 1.5 tube. We tack welded the tube on the left side to the uprights to keep them in line till the were welded I place on the frame then it was removed.
|
|
|
10-01-2013, 09:10 AM
|
#6
|
Senior Member
Join Date: Apr 2012
Location: Elyria
Posts: 108
|
9/5/13 - Day 22
Not as smooth as I hoped but one wall is up.
|
|
|
10-01-2013, 09:16 AM
|
#7
|
Senior Member
Join Date: Apr 2012
Location: Elyria
Posts: 108
|
9/6/13 - Day 23
Wall two is up and roof supports going in.
|
|
|
10-01-2013, 09:30 AM
|
#8
|
Senior Member
Join Date: Apr 2012
Location: Elyria
Posts: 108
|
9/22/13 - Day 39
The wall were mainly tack welded so over the last week, everything got fully welded then all surface welds had to be ground smooth. In the meantime, we had to cover it with a tarp. What a pain! The box will be almost 26 ft long.
For leveling jacks, we went with HWH system designed for a Ford chassis. We only had to modify the rear crossbrace as it was too long. 9000 lbs jacks up front, 6000lbs in the rear. Our frame is taller then the Ford so the jacks are 5 inches off the ground further then designed but nothing a 4 x 4 pad won't fix if the ground is very bad. This thing will mainly be at drag strips which are about as flat as you can get!
|
|
|
10-01-2013, 09:51 AM
|
#9
|
Senior Member
Join Date: Apr 2012
Location: Elyria
Posts: 108
|
9/25/13 - Day 42
For the roof underlayment, we used 3/4" plywood so if we want to, we can walk on it as an observation deck. We made our box 101" wide to get the most space possible. My suggestion to anyone thinking of a similar build, go with 96". A 4 x 8 sheet will not work for our roof, floor or ceiling without adding a small filler piece. That sucks.
The lower compartment rear wall welded in place. Trailer hitch was fabricated and bolted in place earlier.
|
|
|
10-01-2013, 10:02 AM
|
#10
|
Senior Member
Join Date: Apr 2012
Location: Elyria
Posts: 108
|
9/26/13 - Day 43
In our "spare" time we have been screwing and tack welding in sheet metal under the floor tubes. That's to hold the rigid insulation and to act as the lower compartment ceiling. I did a lot of this welding so not all of them are the prettiest. Glad it all gets covered and no one will ever see them. I can MIG something like this but I don't do any of the structural stuff. All the edges will be filled with Great Stuff when the insulation goes in to seal it all.
|
|
|
10-01-2013, 11:55 AM
|
#11
|
Senior Member
Join Date: Sep 2010
Location: Willamina Or
Posts: 277
|
Very nice. Having extra minds to help solve problems is a big plus. How long have you been working on it? How big of a race trailer will you be pulling? Keep up the good work and for sure keep the pictures coming.
|
|
|
10-01-2013, 03:33 PM
|
#12
|
Senior Member
Join Date: Aug 2009
Location: Rockford
Posts: 490
|
looks great. just keep making sure every thing stays straight. i made mine 102" wide. ran roof boards crossways. had more seams but. i was worried about seam down center.
|
|
|
10-01-2013, 11:11 PM
|
#13
|
Senior Member
Join Date: Feb 2009
Location: St. Paul, MN
Posts: 1,819
|
Wow, looks great. Thanks for the thread.
__________________
'03 Freightliner FL112, 295" wheel base, with '03 United Specialties 26' living quarters, single screw, Cat C12 430 h/p 1650 torque, Eaton 10speed , 3.42 rear axle ratio
|
|
|
10-02-2013, 09:02 AM
|
#14
|
Senior Member
Join Date: Apr 2012
Location: Elyria
Posts: 108
|
Quote:
Originally Posted by Kenn
Very nice. Having extra minds to help solve problems is a big plus. How long have you been working on it? How big of a race trailer will you be pulling? Keep up the good work and for sure keep the pictures coming.
|
Ideas have been in the planning stage for a couple years now but each post states the date the work was done. So we have only been working on it 7 weeks.
Trailer is a 34 footer. We are going to be looong.
|
|
|
10-02-2013, 09:39 AM
|
#15
|
Senior Member
Join Date: Apr 2012
Location: Elyria
Posts: 108
|
9/27/13 - Day 44
While the rest of the box is not ready for siding, we did the back panels to get a feel for it. We are using 3M'S 560 adhesive to hold the panels to the steel and using UHB tape at the panel to panel lines. We wanted to use the tape on the seams so they would be clean with no adhesive spilling out. We sanded each upright and cleaned everything with lacquer thinner. It suggests roughing up the panels but we did not. The plastic film on the panels was peeled back to expose the edge but will not be pulled total off till we are totally finished. Its early in the process, but the tape wins over the adhesive. Once the panel is pressed into the tape, you are not going to move it. Better have it in the right spot. With the adhesive, the panel will side all over the place so you have to come up with a way to hold it in place. We clamped tubing under the bottom rail so the panel rested on it and lightly clamped the open sides. Didn't get pics of this process but will when we get to the rest of the box.
|
|
|
10-02-2013, 09:55 AM
|
#16
|
Senior Member
Join Date: Apr 2012
Location: Elyria
Posts: 108
|
9/30/13 - Day 47
Using liquid nails, we glued the one piece aluminum to the roof and used 2 x 4's and bar clamps to hold it in place. Since the roof is 101" and the aluminum 102.5", I bent it over the edge the next day. Not pretty but the trim will cover it. Didn't want to do this now but with several days of rain coming and now several holes in our tarp, it needed to be done.
|
|
|
10-08-2013, 09:21 AM
|
#17
|
Senior Member
Join Date: Apr 2012
Location: Elyria
Posts: 108
|
10/6/13 - Day 60
We have spent the last week dodging rain drops and trying to get the lower compartments welded into place. The generator goes in the compartment behind the drivers side rear tires. We used perforated plate on the back wall and floor to let air to circulate in that area. The rest will mainly be 18 gauge sheet metal with 16 gauge in the wheel wells.
|
|
|
10-16-2013, 09:57 AM
|
#18
|
Senior Member
Join Date: Apr 2012
Location: Elyria
Posts: 108
|
10/10/13 Day 57
Got the propane grill mocked up.
|
|
|
10-16-2013, 10:08 AM
|
#19
|
Senior Member
Join Date: Apr 2012
Location: Elyria
Posts: 108
|
10/12/13 Race Day
We have been trying for a couple years to go faster than 4 seconds in the 1/8 mile and we finally did it. In 660 ft Robert did 3.99 seconds @ 175 mph. Its a 402 cu. in. supercharged small block chevy in a chassis we built. I do the paint work.
|
|
|
10-16-2013, 10:36 AM
|
#20
|
Senior Member
Join Date: Apr 2012
Location: Elyria
Posts: 108
|
10/15/13 Day 62
A couple days of gluing/taping body panels in place. We tack welded a piece under the bottom rail so we could place the panel straight and to hold it till we lightly clamped it. We placed the panel in place, marked door/window location and cut most of them out before gluing the panel up. Still have to cut out the door and the wheel wells but I do like the fender skirt look!. Let it sit at least an hour before we unclamped it and did the next panel. We bounced from side to side and in set up time, we got the tanks installed. Still have the stuff around the cab to do but rain for the next couple days will stop us. We could use a day off any way.
__________________
|
|
|
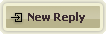 |
|
Posting Rules
|
You may not post new threads
You may not post replies
You may not post attachments
You may not edit your posts
HTML code is Off
|
|
|
|
» Recent Threads |
|
|
|
|
|
|
|
|
|
|
|
|
|