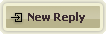 |
|
02-09-2012, 12:44 AM
|
#101
|
Senior Member
Join Date: Sep 2010
Location: Willamina Or
Posts: 277
|
What to make the holding tank out of????
After three days and nights of looking on the net and talking to many people, I have decided to give up the idea of using aluminum. I now plan to build a tank out of plywood with several coats of epoxie. In my search I found ready-made tanks that were close in size but either would not hold as much or were to big to fit my space. I have built many things using wood and epoxie so I know what is ahead of me. I once built gas tanks for a flat bottom boat back it the day. Anyway I did learn that if you need a custom size you need to build it. I always though the big builders used plastic to save money and did not want to spend the time and money to build one out of amuminum.
__________________
|
|
|
02-09-2012, 01:34 PM
|
#102
|
Senior Member
Join Date: Apr 2007
Location: Camano Island, WA
Posts: 163
|
Kenn, what about building the tank out of aluminum and then coating the interior with some type of protective coating, This is pretty much what they do with aluminum drink cans. Would think that an epoxy or perhaps a corrosion coating such as NO-OX-ID ( NO-OX-ID rust preventatives & conversion coating prevent corrosion) could be applied to the interior thru a removable hatch in the top or poured in and then roll the tank around to coat it and drain out the excess. not sure how that would compare cost wise or durability in the elements compared to a plywood tank. I would be afraid of moisture working its way into the plywood from inside or outside and causing delamination or rot. Then again I am way to type A and tend to over think everything lol.
__________________
|
|
|
02-11-2012, 01:12 PM
|
#103
|
Senior Member
Join Date: Sep 2010
Location: Willamina Or
Posts: 277
|
epoxy/wood vs aluminum/????
Dave great minds do think alike LOL. I spent many hours trying to find a product to paint the inside of the aluminum tank. Some concerns I had were not just the tank walls but the aluminum adapter I made. If I coated the adapter with epoxy, it would add enough thickness that the rubber seal would not fit as it should. If I machined the adapter to make room for the epoxy, it would make for a very thin (read weak) part. I checked into pour-in type products and found most are for steel and very little information on aluminum. I am not to worried about water getting to the wood. I will be able to get to all side and the bottom of the tank after the coach is done. If an aluminum tank developed a leak it would have to be removed to make a repair but the wooden tank could at least be glassed over on the outside to get me home. I have used epoxy with good results on many project including boats (gas tanks & and many other areas), race cars body, wings and lots of parts. Yesterday I cut all of the plywood and today I will start on the epoxy. I plan to lay all of the sheets flat and roll and brush the epoxy on before I glue it all together. When the tank is glued together I will do the outside. I really wanted to make it out of aluminum. At some point I need to move on and being the only decision maker I thought the wood/epoxy made the most sence. I will post pictures as the tank develops. Thanks for your thoughts, I do appreciate them. Kenn
|
|
|
02-11-2012, 01:17 PM
|
#104
|
Senior Member
Join Date: Nov 2010
Location: Grafton
Posts: 285
|
What kind of plywood? Marine grade?
__________________
Started looking for 379 Peterbilt TC, 24' to 30' box, bumper pull--but ended up w/1999 Liberty Coach conversion of 45' Prevost XLV bus. 1,000sf heated/AC'd race shop w/dump station, 50amp shore pwr where bus parks, 3 NASCAR/ARCA race cars & 26' Bravo trailer.
|
|
|
02-13-2012, 04:19 PM
|
#105
|
Senior Member
Join Date: May 2011
Posts: 120
|
I have heard of folks building plywood tanks and lining them with fiberglass and it worked OK. Be sure to make the box strong because water is heavy. Containing that water takes a bit of strength when it starts to slosh around.
P.S. I'm not convinced that there would be a problem with aluminum.
__________________
AndyG
1989 FLD120 with 2000 NRC conversion
|
|
|
02-15-2012, 12:54 PM
|
#106
|
Senior Member
Join Date: Sep 2010
Location: Willamina Or
Posts: 277
|
plywood tank
I am using 15/32" exterior grade from Lowes. I am using three layers of 9 once cloth on the inside and two layers on the outside. The inside joints will have an adhesive fillet shaped with a spoon and covered with more cloth. The outside joints will have several layers of cloth. I am installing a tank monitor system made by Tech-Edge Manufacturing in Sweethome Oregon (541) 610-3116. This is a system that mounts foil tape on the outside of the tank and reads through the tank wall. I will be putting the tape on the inside of the tank and running the wires to the outside. The foil tape will be glassed over on the inside.
|
|
|
02-17-2012, 10:44 PM
|
#107
|
Senior Member
Join Date: Apr 2009
Posts: 212
|
Sounds like a good plan. I have done lots of similar work with West Systems epoxy and glass. You are going to need to do something to rough up the surface at the corner jounts since you will have already glassed the inside of the individual plywood sheets. Peel ply is supposed to be an easier way to go but I always just go at it with an auto body disk sander to knock off the shine. The corners need to be extra strong. All that weight will try to bulge out the sides and convert any cube to a sphere.
|
|
|
02-19-2012, 01:59 AM
|
#108
|
Senior Member
Join Date: Sep 2010
Location: Willamina Or
Posts: 277
|
Tech-Edge monitor
Today I epoxied the aluminum strips and copper pads to the inside of the end panel. I drilled a hole and then made small cuts with a hand saw to pass the copper pads through without cutting any wires. I stuck the sensor module to the outside. I used 3" cloth tape and then 4" cloth tape followed with a full layer of cloth. No if I ever needed to change out the sensor it would be possible without going inside the tank. Next up is all of the inlets 1 1 1/2" vent, 2 1 1/2" drains and a 3" toilet going in with a 3" dump valve going out.
|
|
|
02-29-2012, 12:27 AM
|
#109
|
Senior Member
Join Date: Sep 2010
Location: Willamina Or
Posts: 277
|
tank is taking shape
I have been working on the inlets and the outlet for the holding tank. I used stainless thread anchors on the floor of the tank to recieve the 1/4 20 bolts that hold the dump valve to the underside. I used epoxy (thickend) and several layers of cloth on the inside. I will use a good marine sealant on the outside. I made fiberglass flanges to mount the rubber grommets that will hold the abs drains. Today I epoxied the baffel in the center. I will use cloth on the glue joints and then be set to glue the top and bottom on. This has been a big time eating part to build. On the good side it will hold 80 gal.
|
|
|
02-29-2012, 12:31 AM
|
#110
|
Senior Member
Join Date: Sep 2010
Location: Willamina Or
Posts: 277
|
more pics
More pictures.
|
|
|
03-07-2012, 01:24 AM
|
#111
|
Senior Member
Join Date: Sep 2010
Location: Willamina Or
Posts: 277
|
the tank is done
Yesterday I epoxied the drain line flanges to the tank. Today I spent some time trying to clean the shop. I clamped the tank in place and cut, welded, drilled and bolted the mounts to the floor joists. It just fits and fills the compartment except for 8" between the back of the tank and the rear body. The tank ended up weighing 80 LBS and it should hold 79 gallons. I need to drill two more holes after I remove the tank and lower mounts. The tank will have 1/8" rubber between it and the mounts on all sides. I am glad to be done with the tank that was a lot of work.
Tomorrow I will start cutting and welding 2 x 2 for the roof frame. I plan to tack weld it to the floor frame and remove them together. After painting the lower unit and truck I will cut the tack welds and lift the roof add the wall studs.
We have been having rain and snow for a while but tomorrow is going to be sunny so I might move the truck outside and try to clean the shop better.
|
|
|
03-11-2012, 01:08 AM
|
#112
|
Senior Member
Join Date: Sep 2010
Location: Willamina Or
Posts: 277
|
more welding
Today I finished cutting and welding the roof framing. I used .095 2" x 2" on 24" centers for the roof and the floor is .120 2" x 2" on 16" centers welded to the 4" chanel iron. On top of the .120 2" x 2" is .120 1" x 2" laying flat. The first picture is from the rear on the passenger side. Pictures 2 & 3 are showing the roof and floor frames. You can see the 14" frame for the bathroom vent. The last picture is showing how I will store the holding tank until it goes back on the rig. Next up is to cut the tack welds between the two lower sections and lift the top two sections off the truck. I might hang them from the overhead to keep them out of the way.
|
|
|
03-11-2012, 03:10 PM
|
#113
|
Senior Member
Join Date: Apr 2007
Location: Camano Island, WA
Posts: 163
|
Hi Kenn, you have made some real progress, its looking great. For those of you following along at home, my wife and I had a chance to visit Kenn and see the progress on his build personally a couple of weeks ago. This man is doing an amazing job of his build. The truck totally fills his shop, and yet he has found a way to be organized and is efficiently working on a well thought out quality build. Really helps to motivate those of us still stuck in the armchair phase of our builds lol. Thanks again for your hospitality Kenn, and I look forward to pictures of your continued progress, and to my next opportunity to visit with you.
Dave
|
|
|
03-12-2012, 04:05 PM
|
#114
|
Senior Member
Join Date: Sep 2010
Location: Willamina Or
Posts: 277
|
Motivation
Dave thanks for the kind words. Your visit has motivated me to keep plugging along. You asked a lot of good questions. I have been spending time in the planning of the sidewall (FRP) installation. I will clamp one sidewall to the frame and drill .5" holes at four places in the roof frame. I will use .5 steel rods 10' long and run the rods from one side to the other with about nine inches sticking out on each side. Now I will be able to hang the FRP from the rods while I add the glue to the wall studs and frame. After both sides are glued and screwed to the frame I can pull the rods out and fill the holes in the FRP.
|
|
|
03-17-2012, 01:19 AM
|
#115
|
Senior Member
Join Date: Sep 2010
Location: Willamina Or
Posts: 277
|
fender wells
Today I finished the rear fender wells. I started with 32" x 68" 14 ga steel and had the supplier bend a 90 degree bend at 17". I end up with a 17" vertical piece and a 51" horizontal part that covers the tires. The drivers side is 9" longer. The front rest on top of the compartment frame in front of the tires. I made small angle iron tabs with a 1/2" lock nuts welded to them. I drilled holes in the sheet steel and bolted into the tabs and then welded the tabs to the floor joist. I can remove the fender wells from below. I bolted the bottom of the 17" (back of the fender well) piece to the mud flap mount with four 3/8 bolts. It all went as planed but an extra set of hands would have been good. I hope you can understand the pictures. Just a few more things befor I remove the roof and floor framming.
|
|
|
03-25-2012, 11:53 AM
|
#116
|
Senior Member
Join Date: Sep 2010
Location: Willamina Or
Posts: 277
|
sheet metal work
Yesterday I finished fabricating a storage space for my shore-power cord. I used a six inch deep area above the exhaust to save room in the compartment. It was a three day project that included a lot of drilling, welding, sheet metal cutting and head scratching. I think it will work pretty good. I mounted the rubber fender lips and started making a filler plate to cover the eight inch hole below the entry steps when they are retracted for travel. Yesterday was the first day without rain or snow in about a week so I was able to move the truck outside and get better pictures. Next up is to mount the camper frame to casters and store it outside until later. Once the camper frame (floor & roof frame) is out of the way I will remove the lower unit and start getting it ready to paint.
|
|
|
03-25-2012, 12:15 PM
|
#117
|
Senior Member
Join Date: Nov 2010
Location: Grafton
Posts: 285
|
Quote:
Originally Posted by Kenn
Yesterday I finished fabricating a storage space for my shore-power cord. I used a six inch deep area above the exhaust to save room in the compartment.
|
I presume the cord will go in the 6" deep area above the exhaust. With the exhaust below, won't that area get awfully warm? Will the 6" area be open to the compartment next to it? or will there be a cover of some type.
Keep up the good work.
__________________
Started looking for 379 Peterbilt TC, 24' to 30' box, bumper pull--but ended up w/1999 Liberty Coach conversion of 45' Prevost XLV bus. 1,000sf heated/AC'd race shop w/dump station, 50amp shore pwr where bus parks, 3 NASCAR/ARCA race cars & 26' Bravo trailer.
|
|
|
03-25-2012, 12:40 PM
|
#118
|
Junior Member
Join Date: Sep 2011
Posts: 22
|
Kenn ,where did you purchase your rubber fender lips?
Thx, Patrick
|
|
|
03-26-2012, 11:53 AM
|
#119
|
Senior Member
Join Date: Sep 2010
Location: Willamina Or
Posts: 277
|
questions
# 90 , yes the cord will hang in the area above the exhaust. I will wrap the exhaust pipe with a heat insulator that I have used on race cars. The cord will be open to the compartment. I might make a roller for it and pass the end of the cord through the side of the body.
Patrick, I got the rubber fender molding from Esley Truck Accessories located at 8983 Truckman way, Salem Or 97303 phone 1-800 547-3667. They carry two types. The one I used mounts to the outside of the body and the other mounts to a lip around the wheel opening. They are sold by the foot $2.75 for the one I got and $4.50 for the other.
|
|
|
03-27-2012, 08:16 AM
|
#120
|
Senior Member
Join Date: May 2011
Posts: 120
|
This is awesome. Wow!
__________________
__________________
AndyG
1989 FLD120 with 2000 NRC conversion
|
|
|
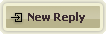 |
|
Posting Rules
|
You may not post new threads
You may not post replies
You may not post attachments
You may not edit your posts
HTML code is Off
|
|
|
|
» Recent Threads |
|
|
|
|
|
|
|
|
|
|
|
|
|